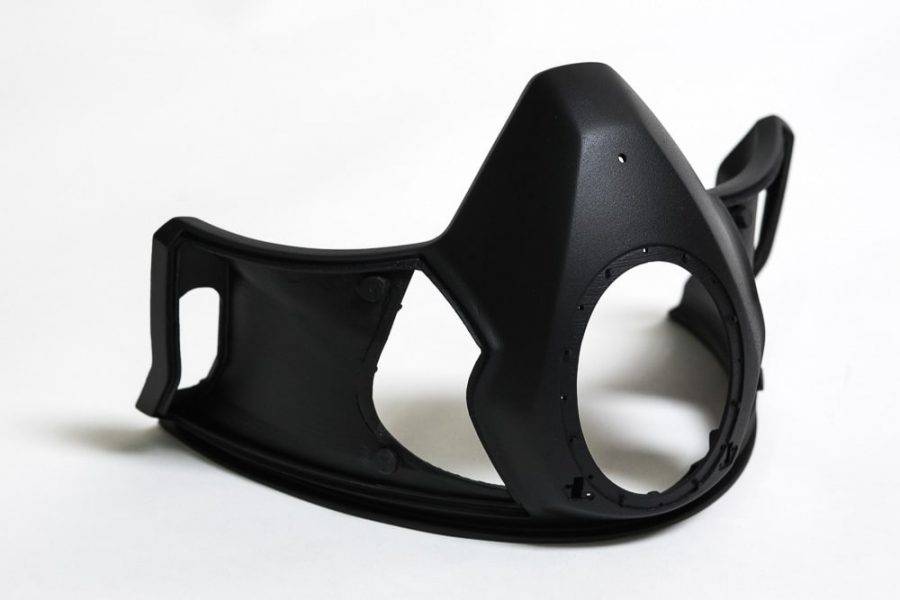
Fused Deposition Modeling (FDM)
We started a three-part blog series based on exploring a few, main 3d printing technologies we, at Dinsmore, provide. So far we have explored, Stereolithography (SLA), which we previously discovered was the most common and most popular form of 3d printing. Continuous Liquid Interface Production (CLIP), a relatively new technology, but it’s able to produce final product quickly and with a smooth-to-the-touch surface. Our final, popular 3d printing technology to explore is Fused Deposition Modeling (FDM).
FDM, an additive manufacturing technology, is most commonly used for modeling, prototyping and production application. First developed in the late 1980’s, this technology did not become commercialized until 1990. “FDM creates prototypes that can endure extreme climates, exposure to chemicals, and mechanical stress — this is for products that need exceptional durability and strength. It’s best for plastic products that feature fairly solid structures.” Parts created with FDM can immediately be used in high-performance and engineering-grade thermoplastic, which is extremely beneficial for engineers and the like. This is the only technology that produces parts with a high level of product-grade thermoplastics.1
FDM is available in these materials:
- ABS-M30
- Nylon
- Polycarbonate
- Polycarbonate-ABS
- Ultem 9085
SLA, CLIP, and FDM are just a few of the many 3d printing options Dinsmore offers and is another reason why our technology is second to none in the industry. Remember if you have a project, don’t get it manufactured until you’ve seen our prototype as we will make sure everything is right, from the beginning to the end.
1 Source: 3dprintingfromscratch.com